Metallizing Equipment & Thermal Spray Systems
Our range of Thermal Spray Systems has been designed by seasoned professionals to meet heavy coating requirements of metal processing industry. These low maintenance systems are energy efficient and shock protected. These are useful for applying corrosion proof coating with consistent surface finish. High Velocity Control Console HVLP Spray Gun Spray & Fuse Coating Gun Mini Plasma Spray Extension Gun Mass Flow Plasma System.
Types of Thermal Spray Equipment
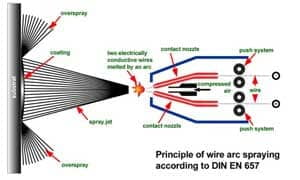
Arc spray coating method is a Thermal Spray process in which two conductive wires are melted as they are acted upon by an arc. The arc produces such a temperature that it transforms the wires into a molten state. The resulting material is then atomized into small particles and ultimately propelled onto the desired substrate by ultra-clean, compressed air. Major advantages of utilizing the wire arc spray coating method include lower operating costs, higher material output per hour, and production of a more coarse coating than the Plasma or HVOF coating methods. As well, wire arc coatings are exceptionally suited for dimensional restoration of both mis-machined and worn parts, saving clients large amounts of time and money; when such events occur. wire arc spray coatings also have a rich history of proven and cost-efficient corrosion protection.
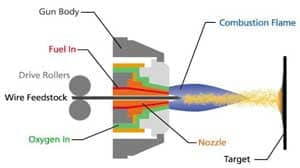
Flame spraying is primarily used to apply abradable coatings or nickel/chrome self-fluxing alloys which are subsequently heat treated to metallurgically bond them to the substrate (Fused coatings). Abradable coatings are used for machine element clearance in compressors. Fused coatings are extensively used in high wear applications such as mining and steel industries to prevent wear of rolls, pistons and other equipment in aggressive wear environments. A Flame Spray gun uses oxygen and fuel gases to produce a flame into which powder is injected. The resultant molten particles of powder are projected on to the work piece to produce the coating. Many coatings sprayed by this process are then heat treated at around 1000ºC to ‘fuse’ the coatings to the substrate surface. Fused coatings produced by this process are hard and corrosion resistant and are able to withstand wear by abrasion, fretting, cavitation and other hard surfaces. The addition of different proportions of carbon, silicon and boron to the basic nickel/chromium alloy results in the formation of hard phases of carbides, silicide and borides.

Plasma Spray Plasma Spraying Process, the material to be deposited (feedstock) — typically as a powder, sometimes as a liquid, suspension or wire — is introduced into the plasma jet, emanating from a plasma torch. In the jet, where the temperature is on the order of 10,000 K, the material is melted and propelled towards a substrate. There, the molten droplets flatten, rapidly solidify and form a deposit.
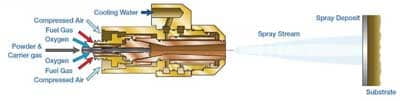
HVOF Spray A mixture of gaseous or liquid fuel and oxygen is fed into a combustion chamber, where they are ignited and combusted continuously. The resultant hot gas at a pressure close to 1 MPa emanates through a converging–diverging nozzle and travels through a straight section. The fuels can be gases (hydrogen, methane, propane, propylene, acetylene, natural gas, etc.) or liquids (kerosene, etc.). The jet velocity at the exit of the barrel ( 1000m/s) exceeds the speed of sound. A powder feed stock is injected into the gas stream, which accelerates the powder up to 800m/s. The stream of hot gas and powder is directed towards the surface to be coated. The powder partially melts in the stream, and deposits upon the substrate. The resulting coating has low porosity and high bond strength.
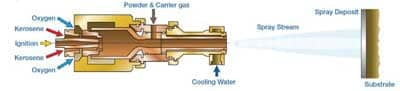
HVOLF Spray A mixture of gaseous or liquid fuel and oxygen is fed into a combustion chamber, where they are ignited and combusted continuously. The resultant hot gas at a pressure close to 1 MPa emanates through a converging–diverging nozzle and travels through a straight section. The fuels can be gases (hydrogen, methane, propane, propylene, acetylene, natural gas, etc.) or liquids (kerosene, etc.). The jet velocity at the exit of the barrel ( 1000m/s) exceeds the speed of sound. A powder feed stock is injected into the gas stream, which accelerates the powder up to 800m/s. The stream of hot gas and powder is directed towards the surface to be coated. The powder partially melts in the stream, and deposits upon the substrate. The resulting coating has low porosity and high bond strength.